Semiconductor leader successfully avoided an estimated USD 6.3 million in losses with DPM CMS solution
Case Study : Semiconductor Industry
Location : Taiwan
Background
Challenges
Solution for Dry Pump
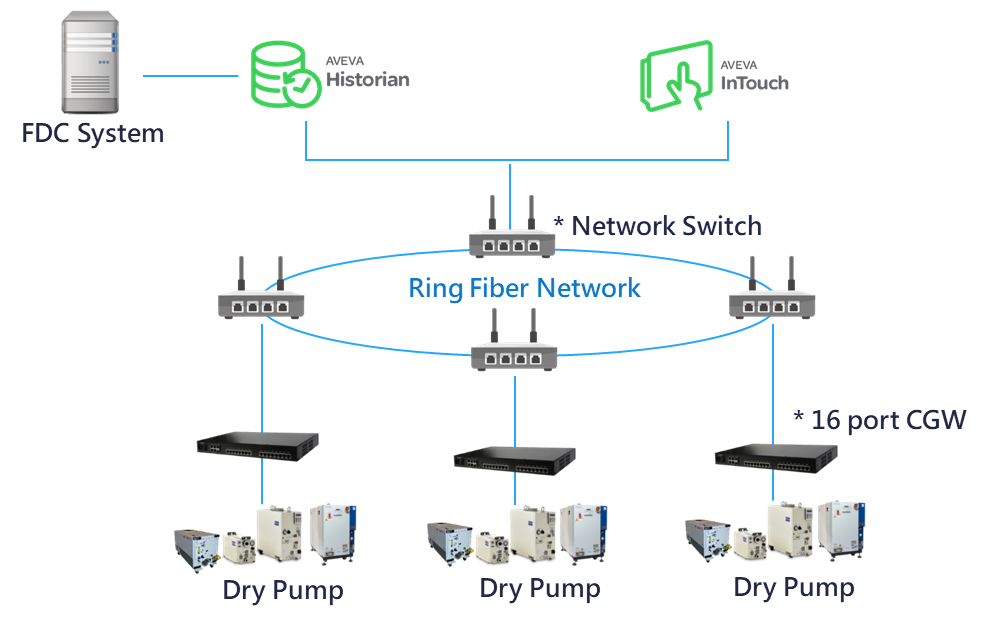
- Each dry pump had an independent isolated communication line to dedicated CGW(Intelligent Industrial Gateway) ports, increasing data transmission speed and reducing impact of disconnections.
- Implemented redundant ring network backbone with CGW smart gateways as control centers, transmitting pump operation status to facility control room and FDC system via message bus.
- InTouch HMI software installed on SCADA terminals received data collected by CGW smart gateways via standard Modbus protocol, providing integrated pump status monitoring for duty personnel
Solution for Local Scrubber
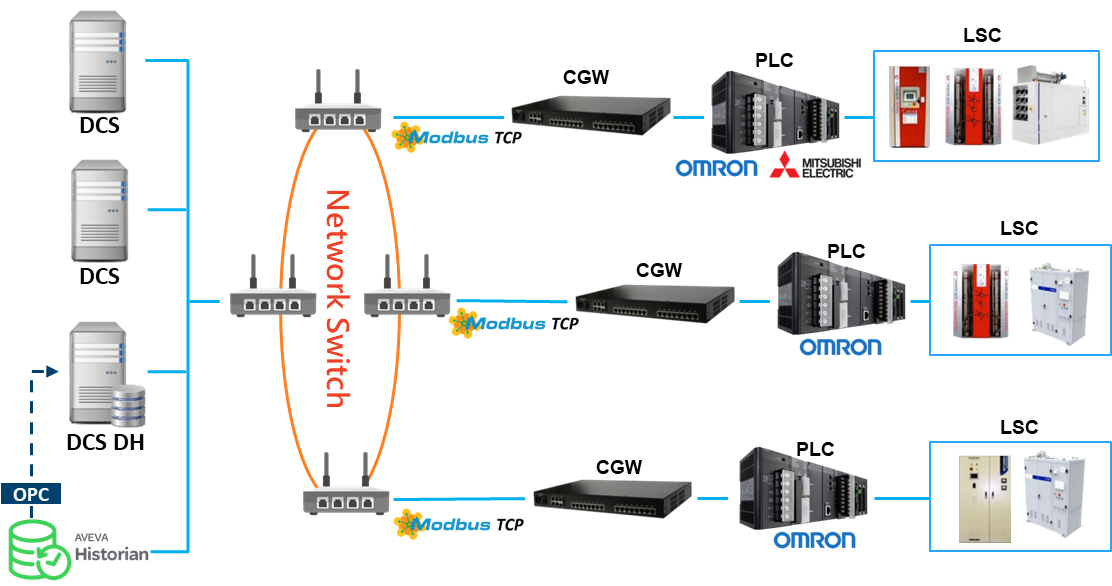
- Implemented CGW for communication connection and data collection from equipment-side PLCs and controllers.
- All LSC (Local Scrubber) equipment values were similarly collected through CGW from equipment-side PLCs and controllers.
For both Dry Pump and LSC issues, CGW was utilized to reduce computer-to-equipment and PLC connections, decreasing system load.
This was expected to improve system stability and connection quality while integrating various communication protocols into a single solution.
Benefits
Simplified Architecture, Stabilized System
Successfully integrated diverse protocols for Dry Pumps, LSC, and PLCs.
Connection issues due to system overload virtually eliminated after CGW implementation.
Reduced Downtime Risk, Rapid Maintenance
CGW replaced vendor-specific monitoring computers, significantly reducing crash risks and enabling quick restoration of Dry Pump and Local Scrubber operations.
Value Creation
Real-Time Failure Prevention
At the first year after implement, the mechanical department precisely intercepted 17 pre-pump failure trends and notified sponsors. Analysis showed the system could accurately capture abnormal pump operation alarms, immediately notify sponsors for condition assessment, and execute contingency measures, minimizing damaged wafer quantities.
Risk Mitigation : $6.3M USD Annual Savings
Based on past experience, approximately 50 pump failures per year had insufficient information for cause determination. Assuming 11 incidents in a quarter * 4 (per year) * 25 wafers/lot * 180,000 NTD = 200 million NTD ≈ 6.3 million USD, this represents preventable losses through the new system.
Get our free ebook on how you can level up your B2B SaaS content marketing
Get our free ebook on how you can level up your B2B SaaS content marketing