Dry Pump Central Monitoring System
(DPM CMS)
Utitech's DPM CMS solution delivers an integrated monitoring solution that unifies thousands and multi-vendor vacuum pumps, enhancing real-time control and semiconductor manufacturing efficiency.
Existing CMS System Issues
Issues
- The old system lacked real-time communication, delaying timely process defect corrections.
- No historical data query mechanism in any systems, resulting in insufficient data granularity for process analysts to effectively analyze incident causes.
- Unable to predict pump status in real-time, leading to unplanned equipment downtime and impacting product yield.
- Different equipment and application systems had inconsistent operating logic and alarm display methods.
- System applications couldn't be modified or expanded independently, causing maintenance difficulties.
- After system implementation, vendors' lack of application maintenance.
- capabilities often delayed normal system operation.
Challenges
- To meet different process requirements and risk distribution needs, thousands of dry pumps from different manufacturers were used, each with different communication protocols and interfaces.
- Traditional CMS (Central Monitoring System) computers could only connect to 40 pumps each, while semiconductors in Taiwan required capacity for 62.5 times more equipment.
- Single SCADA software was limited to 200-300 connection points, while semiconductors in Taiwan required over 10 times that capacity
Scalable Architecture for Unified Dry Pump Communication and Control
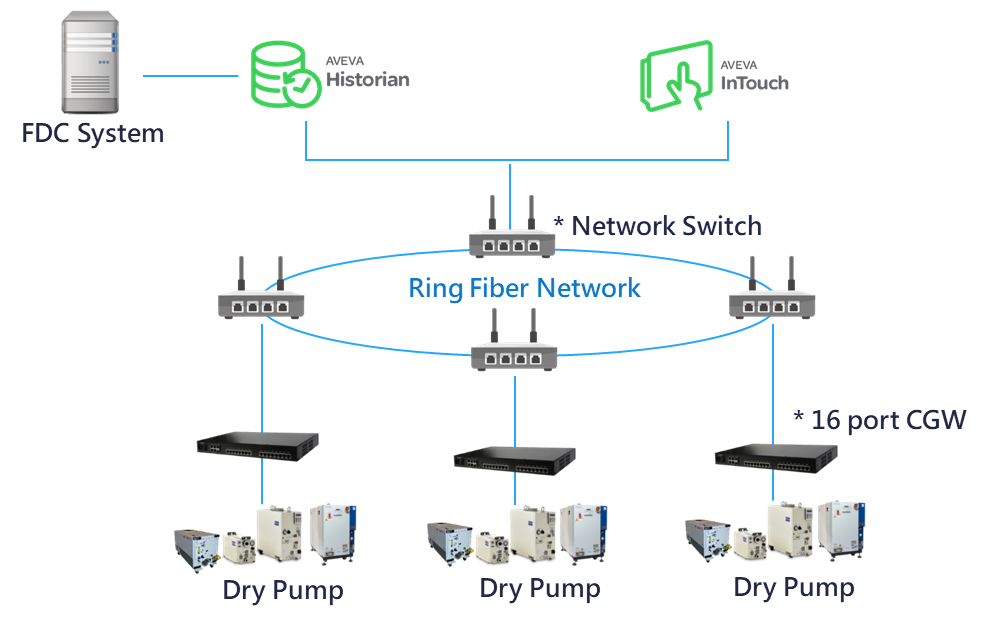
Replace
Implemented multi-serial port devices to replace vendor-provided PCs, preventing hard drive failures and enabling rapid restart within seconds. The device can connect to sixteen pumps of different brands, models, and protocols.
Single connection
Single-port connection facilitates rapid pump replacement during maintenance or failure events.
Redundancy
Two backup monitoring computers observed all facility pumps and recorded long-term operational alarms and data.
Unify
All equipment connected via Ethernet to the supervisory system, operating under unified logic regardless of brand or model, meeting sponsor requirements.
Implement Results
-
Real-time Information Display
-
Improved Communication Efficiency
-
Enhanced Maintenance Capability
Each dry pump had an independent isolated communication line to dedicated CGW smart gateway ports, increasing data transmission speed and reducing impact of disconnections.
- Unified integration of dry pumps from different vendors.
- S-CMS built on open platform architecture with available source code for faster, more complete maintenance.
- Implemented redundant ring network backbone with CGW smart gateways as control centers, transmitting pump operation status to facility control room and FDC system via message bus.
Value Creation
- Long-term data accumulation in databases enabled verification of vendor-claimed equipment reliability parameters (MTBF, MTTR) through reporting tools, maximizing equipment uptime.
- Real-time monitoring information enabled equipment utilization analysis, examining downtime causes, frequency, and duration to improve and reduce downtime, thereby increasing production equipment uptime.
Get our free ebook on how you can level up your B2B SaaS content marketing
Get our free ebook on how you can level up your B2B SaaS content marketing